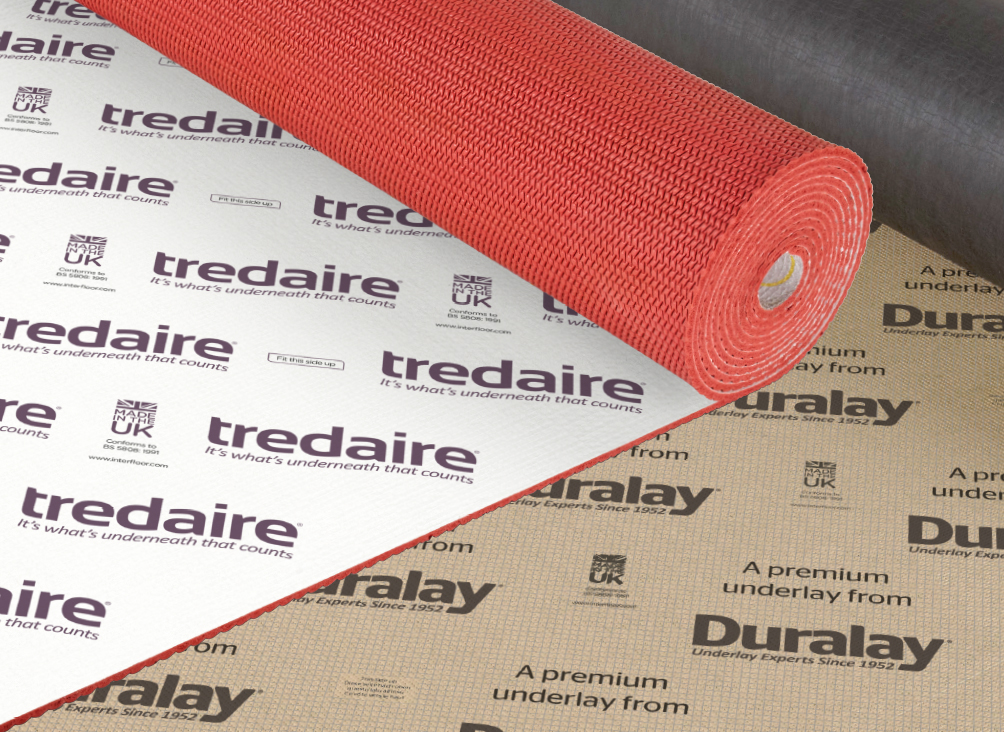
After experiencing a strong start to the year, like all companies in our industry, we then had to cope throughout March, April, & May with all the uncertainties & concerns brought about by Covid 19. But with retailers now open and consumer demand strong, the business is looking forwards to a busy next six months.
Interfloor was quick to respond when the UK government advised all non-essential businesses they should close to stop the spread of coronavirus back in March. And the Interfloor team has been equally quick to ramp up its operations as soon as demand looked likely to return, building up stock and implementing new health and safety measures to ensure they could cope with that demand as soon as those first green shoots of recovery emerged.
Keen to deal efficiently with pent-up demand for its market leading underlay and accessories from the Tredaire, Duralay, Gripperrods and Stikatak brands, the team worked diligently to ensure customers received their deliveries quickly.
CEO John Cooper said: “Taking our logistics operation in-house at the start of the year has proved an absolute game-changer for Interfloor during this year’s unprecedented events. The change has allowed us to be more agile in responding to customers’ needs and more integrated across our whole supply chain.
“Safeguarding the team and our customers has been a priority. Quite early on we implemented new health and safety measures to ensure our workplaces remained low-risk. Everyone has responded well and we’ve had some very positive feedback from customers who appreciate our efforts to get back to business as usual as soon as possible. We’ve coped well to meet demand and strong trading since mid-May.”
With a worldwide customer base, Interfloor has also continued to supply major export projects throughout lockdown. Its popular British-manufactured brands are sold to flooring contractors, retailers and distributors in over 70 countries.
This was facilitated by changes to the way Interfloor operates its manufacturing site including staggered shift start times and the creation of new safe walkways, with clear markings and one-way systems around the site to ensure people could socially distance in all areas. More rest areas and rescheduled break times have been introduced, and workstations clearly marked. PPE equipment and personal hand sanitiser has been provided, and additional cleaning supplies have been made available for wiping down shared equipment and rest areas.
“Maintaining high levels of hygiene has been crucial in professionally managing the spread of the virus. We temperature check everyone on entering the site each day, all our employees have been working according to social distancing where possible, and we’ve given both employees & visitors ample time & opportunity to increase hand-washing routines when on-site. Everyone has adapted well to the new routines and I’d like to thank them all for their rigorous application of our new protocols,” added John.